
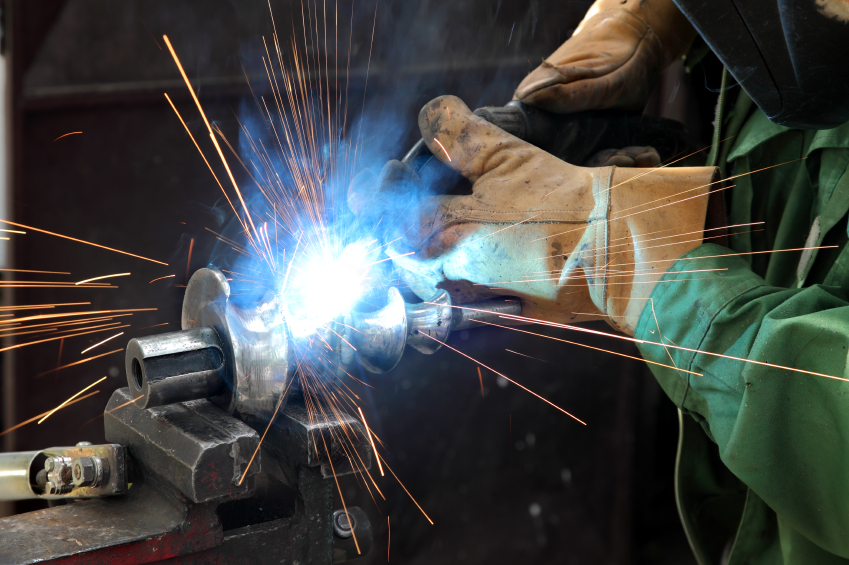
Miller has made things easier with the introduction of not only its 212 Auto-Set MIG, on which you simply set the wire size and metal thickness before welding, but also with the revolutionary Diversion 165 AC/DC TIG, on which you just set the material type and thickness. TIG welding is more complicated and until recently the bewildering array of knobs and switches on a TIG welder meant you had to really know what you were doing to set the machine up. Whether you're learning to MIG or TIG, you're going to have to master the machinery, though most MIG welders these days carry a chart inside the casing where the wire spool mounts, guiding you to the correct wire speed and heat settings for the thickness of metal you're planning to weld. TIG welds are smaller, neater and of higher quality than MIG welds, and are what we have come to expect when we see high quality, precision fabrication and chassis work. DC (direct current) is usually used for welding stainless steel and mild and low alloy steels, while AC (alternating current) is used for welding aluminum. If the electrode touches the work it becomes contaminated and must be cleaned immediately, which can be frustrating while you learn to TIG weld, as you'll spend more time removing and cleaning the electrode than actually welding until you get the hang of it! The power source is constant current, either AC, DC, or combination of both (AC/DC), with the type of metal being welded determining which type is used. However, the work surface has to be extremely clean for TIG welding, especially when welding aluminum, and it is a relatively slow process.

Unlike MIG, the operator can adjust the heat input whilst welding by using the foot-operated amperage control pedal. TIG welding produces no spatter either, unlike MIG can sometimes do, and the torch is smaller and therefore easier to hold and work with.
